Case Study: Repair of Leaking 350mm Effluent Pipe Running out to Sea Underneath Salt Marshes
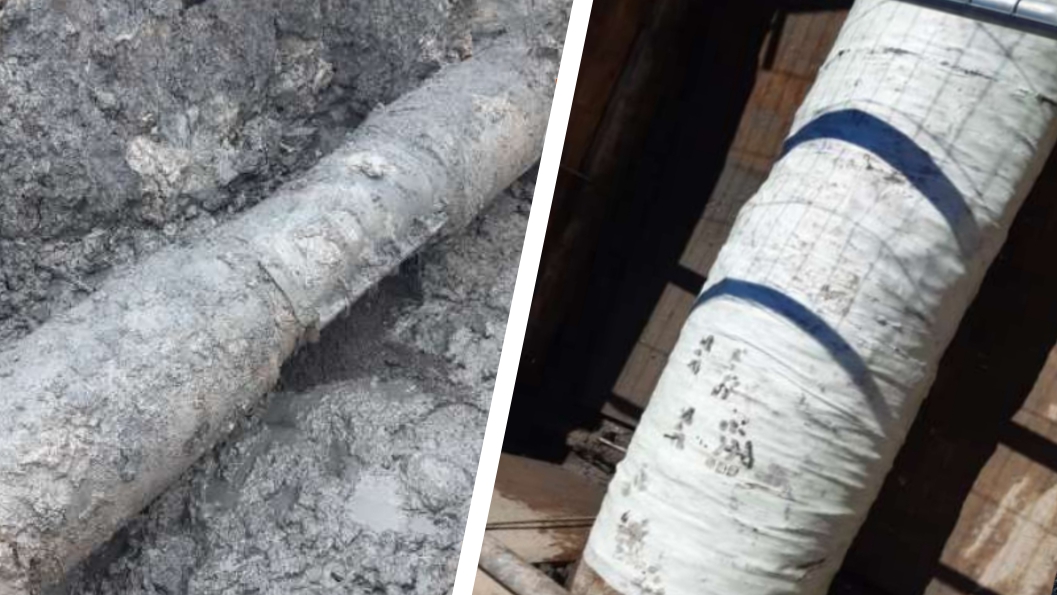
Against the tide – the leaking pipe beneath salt marshes that had to be sealed in under eight hours
A chemical plant in the UK faced a logistically challenging repair, needing to seal a leaking 350mm effluent pipe running underneath salt marshes and out to sea with only an eight hour timeframe to work whilst the tide was out.
Case Study Data
Site
Chemical plant
Location
United Kingdom
Repair Type
No pressure leak repair
Defect
Corroded steel pipe leaking in numerous areas from a defective clamp
Products Used
Sylmasta AB Original Epoxy Putty
Super-strength, waterproof epoxy putty capable of sealing leaks underwater and in aggressive environments
SylWrap HD Pipe Repair Bandage
Composite repair wrap which sets rock hard in minutes to reinforce leak repairs and strengthen and protect pipelines
Case Study PDF
Case Study Details
The 350mm steel pipe carried effluent from the chemical plant underneath salt marshes and out to sea. It had undergone a repair just one year earlier, which was now discovered to have failed.
When originally installed in the 1960s, the steel had been coated in cement for reinforcement. The previous repair had consisted of removing part of the cement and covering the heavily corroded and perforated section of steel pipe with a clamp.
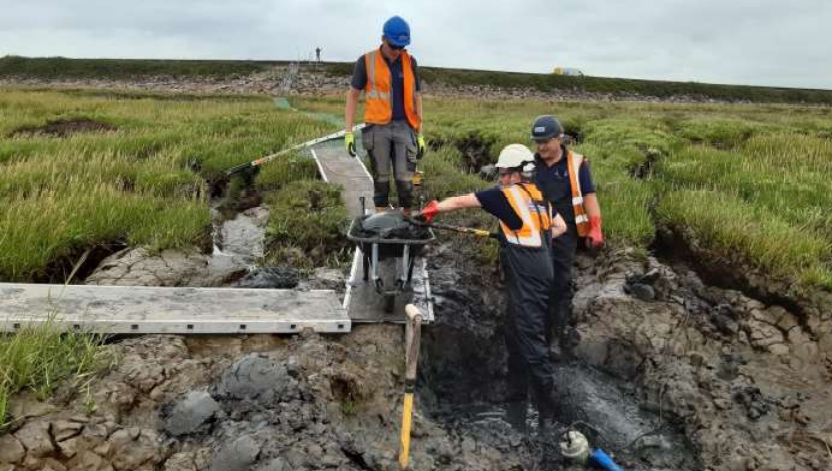
The line’s location under the salt marshes made any repair logistically challenging. The pipe could only be accessed when the tide went out, after pumping away seawater and then digging by hand through sludge. No heavy tools or machinery could be transported onto the marshes to help dig as it would simply sink.
When nature ran its course and the tide then came back in, the pipe was flooded again and so the process had to begin from scratch. This left only an eight hour window in which the pipe was under dry conditions and could be worked on.
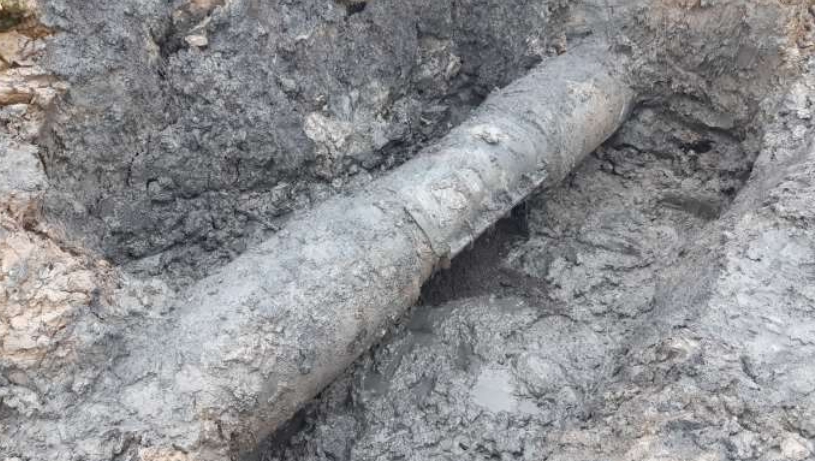
The chemical plant appointed a specialist marine engineering contractor to formulate a repair method. First, the pipe was excavated for inspection. This revealed it to be leaking from both ends of the pipe repair clamp.
To complicate matters further, the steel had now deteriorated significantly. The wall of the pipe was so thin beneath the clamp that the contractor was concerned removing the original repair could have led to the collapse of the line.
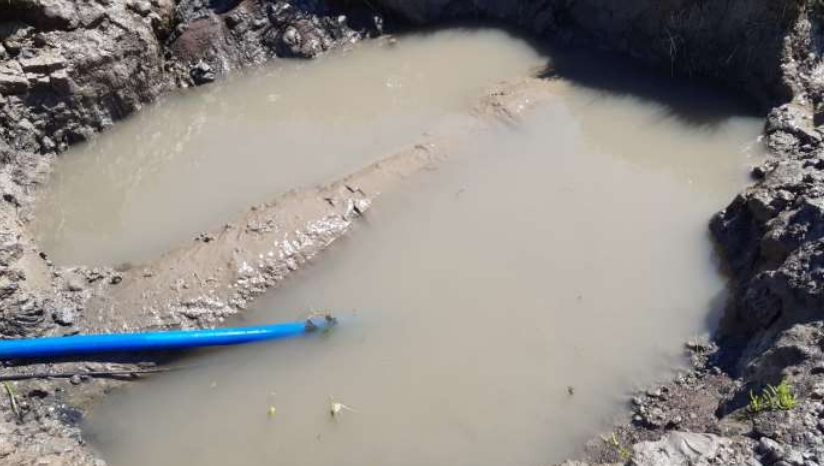
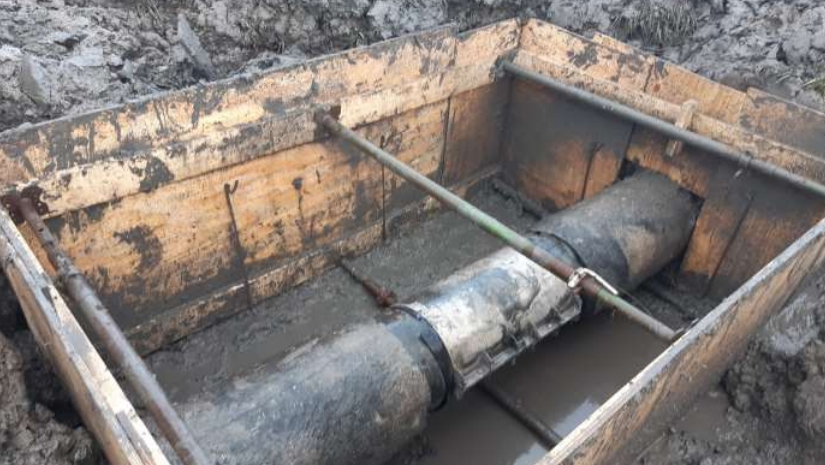
The contractor consulted Sylmasta, who recommended encapsulating the clamp with a waterproof material to seal it. Further protection could then be provided with a composite wrap. All products used in the repair had to be applied and functional quickly because of the short timeframe in which the pipe was accessible.
As soon as the tide went out, the process of excavating the pipe began again. Sludge was removed from the hole and water pumped away. A temporary wooden framework was built around the pipe to create a safe working area. Sylmasta AB Original Epoxy Putty was then applied around the entire clamp for the purpose of sealing the leak areas.
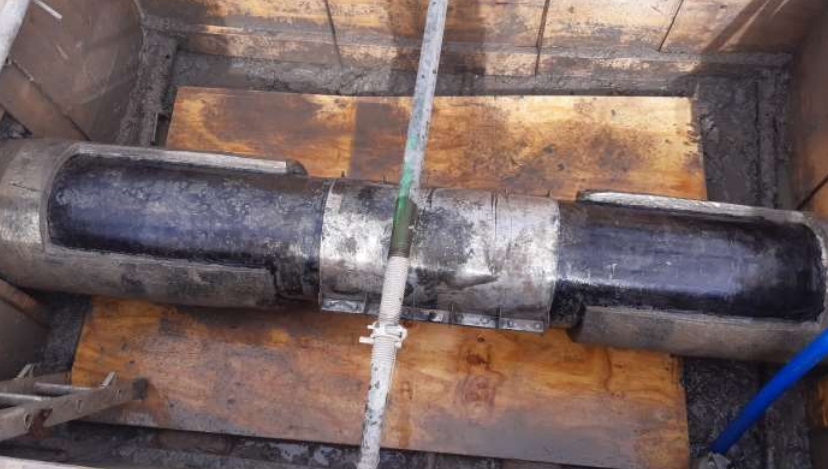
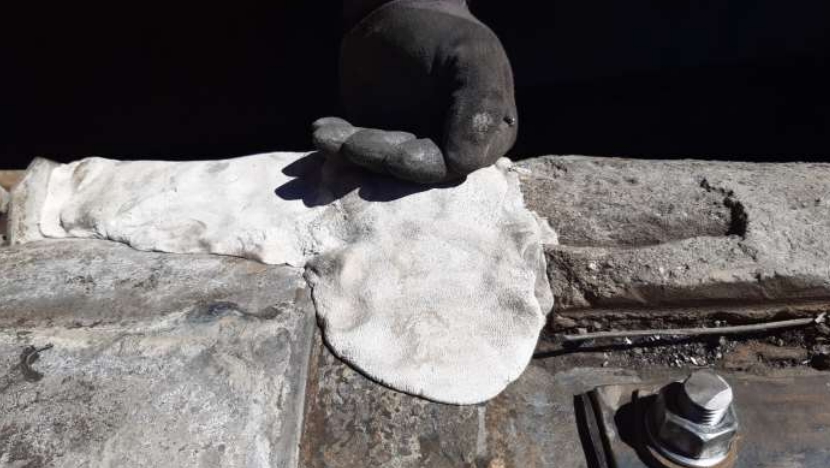
AB Original is a waterproof, super-strength epoxy putty with a two hour work time. Once cured, it would easily withstand the harsh environment of the salt marshes. The putty was mixed by hand and pushed onto the clamp, filling all holes and cracks through which effluent had previously escaped.
Two inspection hatches were then cut into the steel pipe either side of where the putty had been applied, so the inside of the line could be accessed. Reaching through these hatches, the contractors were able to coat the interior of the pipe with a liquid metal epoxy coating.
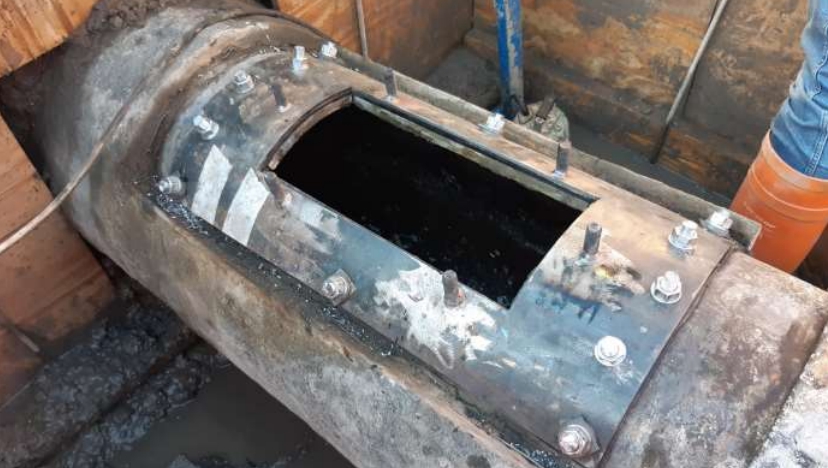
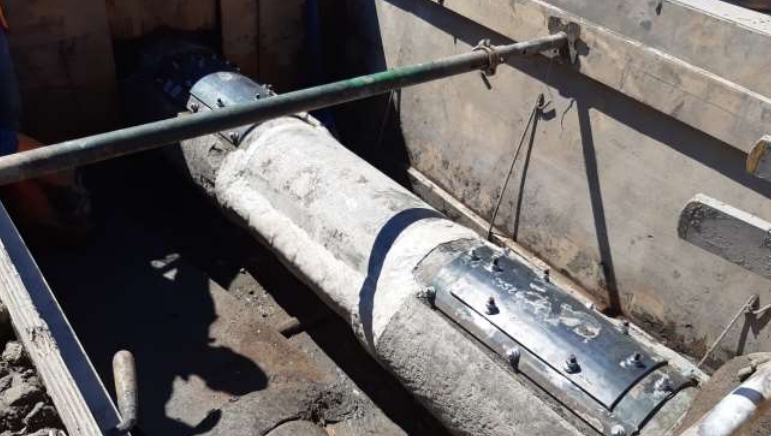
Liquid metal cured inside the pipe to provide a new metallic lining, increasing the sealing security of the repair and restoring wall thickness. The two inspection hatches were then fitted with cover plates and firmly sealed.
A concrete coating was next reapplied over the pipe, and the entire excavated section wrapped with several layers of SylWrap HD Pipe Repair Bandage. SylWrap HD is a water-activated composite wrap which sets rock hard in minutes.
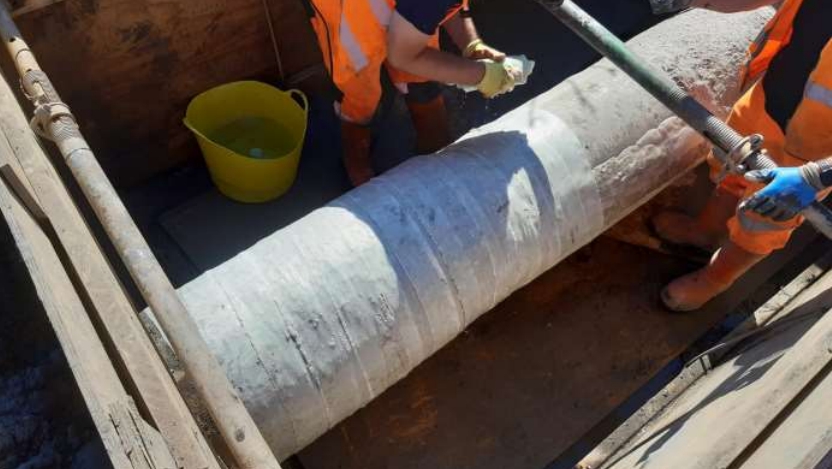
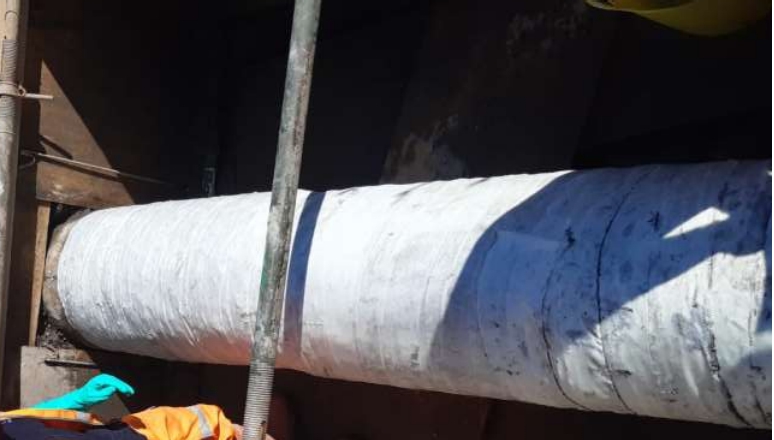
Numerous bandages were smoothed and wrapped around the pipe, curing to form a reinforced protective sleeve. This restored the integrity of the line, uniting and strengthening both the weak and solid areas of the repair.
The speed and ease with which AB Original and SylWrap HD could be applied enabled the application to be completed within the eight hour window. By the time the tide returned to the salt marshes, the pipe had been successfully sealed ahead of being covered with mud and seawater again.
Following the completion of the effluent pipe repair, the contractors told Sylmasta that they were very impressed with the products and the technical assistance provided. They are intending to use AB Original again on a similarly complex application for another client in the near-future.
If you have an application you would like to enquire about, then please get in touch
Call: +44 (0)1444 831 459
Email: sales@sylmasta.com